Building the Future: Innovations in Sandwich Panel Production Lines
china eps lightweight sandwich wall panel production line factory
In recent years, the construction industry has undergone a transformative shift towards more efficient and sustainable building materials. Among these innovations, sandwich panels have emerged as a game-changer, offering a unique combination of insulation, durability, and lightweight characteristics. The production lines dedicated to creating these panels have evolved dramatically, enabling manufacturers to meet the growing demand for energy-efficient solutions in both commercial and residential projects.
As we explore the cutting-edge advancements in sandwich panel production lines, it becomes clear that technology plays a crucial role in enhancing quality and productivity. From automated processes to improved material handling systems, the innovations in this sector are reshaping how these structural components are produced. The focus now lies not only on speed but also on precision and sustainability, driving the industry towards a future that prioritizes both performance and environmental responsibility.
Overview of Sandwich Panels
Sandwich panels are a type of building material characterized by their lightweight yet strong structure. They consist of two outer layers, usually made from metal or other durable materials, with an internal core that can be composed of various insulating materials, such as polyurethane, polystyrene, or mineral wool. This configuration creates a composite design that offers excellent thermal insulation and soundproofing, making them ideal for a range of applications in construction, industry, and infrastructure.
The versatility of sandwich panels has led to their widespread use in commercial buildings, warehouses, and cold storage facilities. Their ability to be produced in different sizes and finishes allows architects and builders to customize panels for specific aesthetic and functional requirements. Additionally, their quick installation process can significantly reduce construction time and labor costs, enhancing overall project efficiency.
In recent years, advancements in production technology have further improved sandwich panel performance and sustainability. Innovations in materials and manufacturing processes are leading to panels that are not only more energy-efficient but also more environmentally friendly. This ongoing evolution in sandwich panel design and production makes them a pivotal element in modern construction practices, reflecting a commitment to both functionality and sustainability.
Technological Advancements in Production
The production of sandwich panels has witnessed significant technological advancements that enhance efficiency and quality. One of the most notable developments is the integration of automated production lines. Automation reduces labor costs and minimizes human error, allowing for more precise control over the manufacturing process. With robots and computer-controlled systems, manufacturers can achieve higher speeds and consistency, ensuring that each panel meets stringent specifications.
Additionally, advancements in materials science have led to the use of innovative core materials that improve the performance of sandwich panels. These new materials, including advanced foams and composites, offer enhanced thermal insulation, fire resistance, and structural strength. By using optimized materials, production lines can produce lighter panels without compromising on durability, catering to the growing demand for energy-efficient construction solutions.
Finally, the implementation of real-time monitoring systems has revolutionized quality control within sandwich panel production lines. Sensors and data analytics allow manufacturers to track the production process continuously, identifying any deviations from the standard immediately. This proactive approach not only reduces waste and defects but also enables quicker response times to production challenges, ultimately leading to superior product quality and customer satisfaction.
Sustainability in Manufacturing
As industries face growing pressure to reduce environmental impact, the production of sandwich panels has begun to shift towards more sustainable practices. Manufacturers are increasingly adopting eco-friendly materials that minimize waste and enhance energy efficiency throughout the production process. These innovations not only help lower the carbon footprint but also appeal to a market that is increasingly aware of sustainability issues.
The introduction of advanced technologies in the sandwich panel production line plays a crucial role in this transition. Automated systems and intelligent manufacturing processes improve precision and reduce material waste, ensuring that resources are utilized more effectively. Additionally, some manufacturers are exploring the use of recycled materials as core components in sandwich panels, further contributing to a circular economy and reducing reliance on virgin resources.
Collaboration with suppliers and stakeholders is vital for sustainable practices to take root within the sandwich panel industry. By working together, companies can create standardized guidelines for sourcing materials responsibly and implementing energy-efficient technologies. This collective effort not only enhances sustainability in the production line but also promotes an industry-wide commitment to environmental stewardship, paving the way for a more sustainable future in construction and beyond.
Automation and Efficiency
Automation in sandwich panel production lines has revolutionized the manufacturing process, significantly enhancing efficiency. Through the integration of advanced robotics and automated machinery, production lines can achieve higher output rates with consistent quality. Automated systems can handle repetitive tasks such as cutting, laminating, and assembling, reducing the need for manual labor and freeing up workers to focus on supervision and quality control.
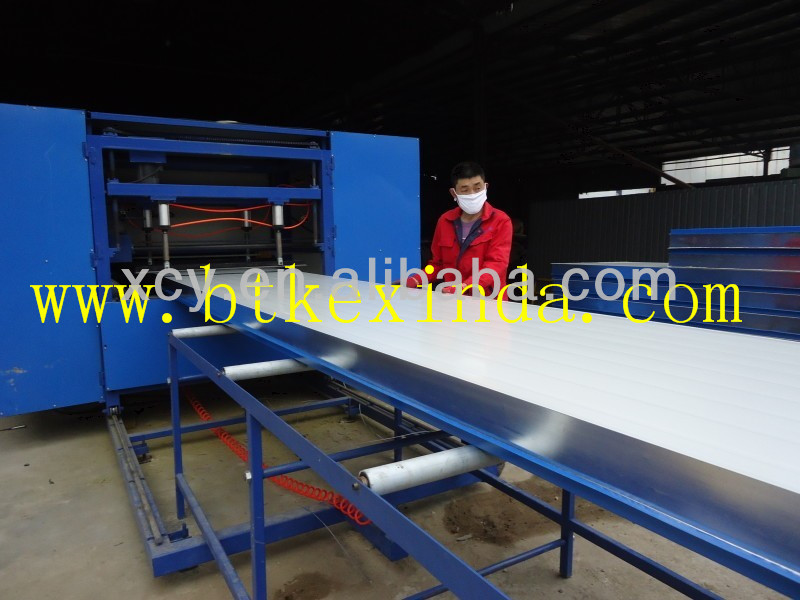
Moreover, smart technology plays a crucial role in optimizing the workflow of sandwich panel production lines. By utilizing sensors and data analytics, manufacturers can monitor equipment performance in real time, identifying potential bottlenecks and maintenance needs before they escalate into costly downtime. This proactive approach not only streamlines operations but also contributes to smarter resource management, ultimately reducing waste and increasing overall productivity.
In addition to enhancing efficiency, automation also impacts the precision of the production process. With technology enabling tighter tolerances and better control over material application, manufacturers can produce sandwich panels that meet stringent industry standards. This level of precision minimizes rework and scrap rates, resulting in a more sustainable production environment and improved profitability for companies in the competitive construction materials market.
Quality Control Measures
Quality control measures are critical to ensuring that sandwich panels meet the required standards for performance and durability. At each stage of the production line, inspections are conducted to verify that the materials and processes adhere to specifications. This includes checking the properties of the core material and outer sheets, as well as monitoring the adhesive application process. By maintaining rigorous oversight throughout production, manufacturers can prevent defects that may compromise the integrity of the final product.
Incorporating advanced technology into quality control can significantly enhance the monitoring process. Automated systems equipped with sensors and cameras can detect anomalies in real-time, allowing for immediate adjustments. This not only improves efficiency but also reduces waste, as faulty panels can be identified and removed early in the production cycle. By leveraging these technologies, companies can achieve a higher level of consistency in their products.
Post-production testing is another essential component of quality control. Once the sandwich panels are fabricated, they undergo a series of tests to assess their thermal resistance, mechanical strength, and overall performance. This ensures that the products fulfill the necessary industry requirements and can withstand various environmental conditions. Regularly reviewing these testing protocols helps manufacturers stay compliant with safety regulations while continuously improving their processes.
Future Trends and Challenges
The future of sandwich panel production lines is poised to embrace advanced technologies that will enhance efficiency and sustainability. Automation and robotics are set to play a significant role, allowing for faster production speeds and consistency in quality. Smart manufacturing processes, driven by artificial intelligence and machine learning, will optimize operations, predict maintenance needs, and reduce waste. As the demand for innovative building materials grows, manufacturers will need to adapt their production lines to accommodate a wider range of materials and designs.
Sustainability will be a core focus as the construction industry moves toward greener practices. The production of sandwich panels is expected to incorporate recycled materials and eco-friendly processes, minimizing the environmental impact. Innovations may also include energy-efficient production methods and partnerships with suppliers committed to sustainability. Challenges such as sourcing sustainable raw materials and ensuring compliance with environmental regulations will require ongoing attention from producers.
Moreover, market competition is expected to intensify as new players enter the field and existing manufacturers strive to differentiate their products. Investing in research and development will be crucial to stay ahead of trends and meet evolving customer demands. Companies that leverage cutting-edge technologies and prioritize sustainability will be better positioned to navigate future challenges in the sandwich panel production line landscape.